
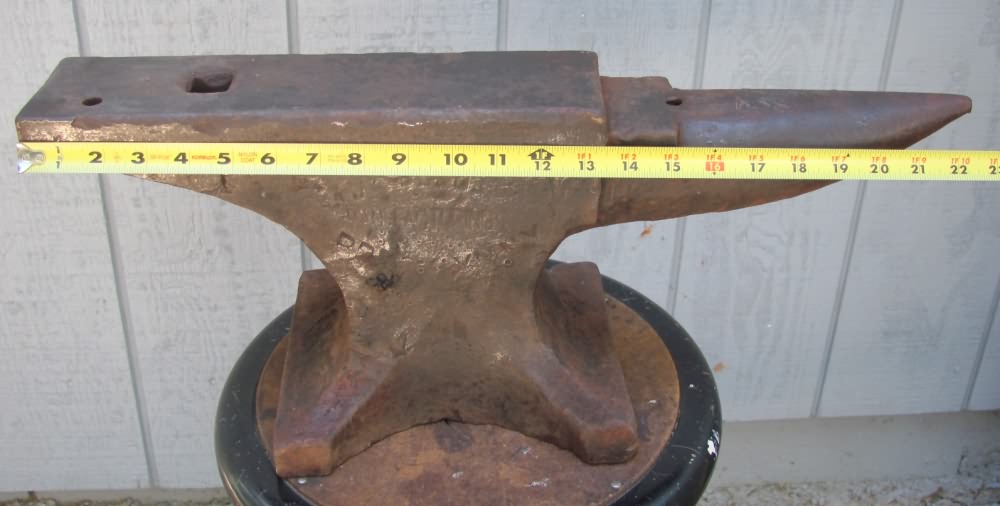
HAY BUDDEN ANVIL HISTORY SERIAL
Thanks for posting the pics of the logo stamp and serial number! Interesting bit of detective work to determine how the anvil was made. Possibly, the body was cast from a mild steel or semi-steel to "take weld" as it did. As I said, I plead ignorance as to the material the body of a Trenton anvil would be made from, but the appearance of the anvil (parting line on the beak or horn of the anvil seems to point to some kind of casting. Whoever welded this anvil at the waist seems to have gotten a good weld, with good fusion and no undercut. Either way, welding wrought iron by processes other than forge welding is a somewhat difficult proposition. Oxyacetylene welding is a process which can give a good weld on wrought iron as the welder can work the puddle to fuse in the wrought iron and float up the slag. Stick welding with a small diameter electrodes using low heat will work, but some of the entrained slag in the wrought iron will often float up into the weld pool. Forge welding is the best process for welding wrought iron. It has a stringy kind of structure with slag laying in the laminations. Wrought iron is not the easiest material to weld using welding processes such as stick or MIG. This would point to the body of the anvil being a mild steel or semi-steel casting. The weld was run using a mild steel filler rod. A weld on cast iron or semi steel would be run with a nickel-based repair rod, and would appear brighter than the base metal and not so neat of a bead. I wonder as to the material of the anvil body. My belief is the anvil had been broken at the waist and re-welded. It has a typical weld bead with a wide weave, and there are "dingleberries" as would come from a poorly run stick weld or MIG weld. Looking at the weld in the photos, I do not think the weld was run when the anvil was originally made. The face plate had "lugs" to "key" the face plate mechanically to the anvil body. A common method was to pour the body of the anvil with something like malleable iron or semi steel, incorporating a tool steel face plate in the casting. I admit to not knowing how Trenton anvils were made. This face plate was then quenched to harden it. The anvil was then forged to nearly final shape, and the steel face plate was forge welded on. Once these pieces were rough-forged, they were forge welded at the waist. These were forged the approximate shape of the top and bottom of the anvil body and horn. The wrought iron was cut into short bars and forge welded to form two large lumps. I am unfamiliar with Trenton anvils, however, a lot of older anvils (Hay Budden, Peter Wright coming to mind) were made with wrought iron bodies. The forge weld was made under steam hammers. Anvils with welds at the "waist" of the body were forge welded.
